tube. Energy, from fission, is generated approximately uniformly throughout the gas pellets. Heat is extracted at the rod surface by the coolant move. The temperature on the hottest level, at the pellet centerline, is often within the vary 800–1000 °C, relying on the ability level. The metallic cladding is an effective conductor, so the temperature rise throughout the wall is just a few tens of degrees.
The melt layer is quite skinny; for instance, when cladding an aluminum alloy it is about zero.5–4μm (Kreye 1985, 1997 ). The dilution of the molten zones results in airplane or corrugated interfaces. During mechanical decladding, the gas assemblies are chopped and the gasoline core is leached with nitric acid, forsaking the undissolved cladding materials for disposal as a solid waste.
The compromise between these competing demands has produced wall thicknesses of ∼zero.9mm in BWRs and ∼0.7mm in PWRs. Laser cladding usually includes covering a relatively inexpensive substrate materials with a costlier alloy that will enhance the resistance of the part to put on or corrosion.
Dissolved oxygen in PHWR coolant is managed between 10–50 ppb and it has been observed that corrosion in both zircaloy-2 and Zr-2.5 Nb stress tubes rises to an exceptionally excessive value at high oxygen concentrations. The BWR coolant normally incorporates a better level of oxygen, sometimes 200–400 ppb.
In one, a second internal-floor liner of ordinary Zry is extruded on the sponge zirconium liner so as to restore corrosion resistance. In other modifications, the sponge zirconium is alloyed with iron or tin to enhance oxidation resistance without affecting the softness that provides immunity from PCI. Standard Zry is sufficiently onerous to be vulnerable to emphasize-corrosion cracking (SCC) when the pellet–cladding hole closes and the swelling gasoline generates substantial tensile hoop stresses in the cladding. In the presence of an aggressive fission product (iodine is most frequently cited), a brittle crack can be initiated and penetrate the cladding wall.
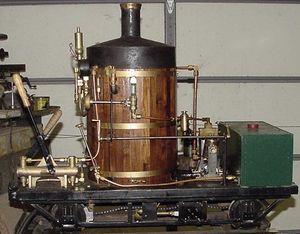
Action for building homeowners

Its business identify is Zircaloy, or Zry for brief. Zry comes in two varieties, Zry-2 and Zry-four. These two differ by minor changes within the concentrations of the transition metals (Zry-4 has no nickel). PWRs use Zry-4 whereas BWRs employ Zry-2 as cladding and either Zry-2 or Zry-four for the duct or channel holding the gas-factor bundle.
Increased wear and oxidation resistance of titanium aluminide alloys by laser cladding Euro Superalloys. Increased wear and oxidation resistance of titanium aluminide alloys by laser cladding. A structured separating layer, consisting of a three-layer vapour-permeable roof underlay membrane with self-adhesive butyl strips, bonded to monofilaments organized in a random community, for use as a spacer layer between the roof construction and the metallic cladding. Those areas subjected to extreme warmth - from the exhaust manifold or catalytic converter for instance - would be insulated by a refractory materials and metallic cladding. Wire-primarily based laser deposition welding is a fabric-efficient 3D printing process for the production of metallic elements.
As a remedy, fast cooling of the Zry ingot throughout fabrication (known as beta quenching) produces a much finer intermetallic precipitate inhabitants. This distribution of the transition metals maintains the power of the Zry but improves its corrosion resistance, probably by short-circuiting cost-transport paths between the dimensions surface and the metal–oxide interface. In order to eliminate waterside corrosion of cladding as a life-limiting process, modified Zircaloys have been developed. Under PWR water circumstances, lowering the tin content material of Zry to 1% and adding a comparable focus of niobium produces an alloy with a corrosion rate several instances decrease than that of the usual Zry. Modified low-tin alloys can be utilized either as a complete alternative for the Zry tube wall or as a thin outer skin on standard Zry substrate tubing.
This is a primary cladding failure that admits steam into the rod with the accompanying potential for a extra critical secondary failure as a result of hydriding. The mixture of situations (vulnerable metallic, tensile stress, and chemical enhancer) that produces the primary defect is termed pellet–cladding interaction (PCI). scale that grows around them during in-reactor operation. This lack of the insulating properties of the oxide is believed to accelerate the corrosion fee.
Joining happens repeatedly by local plastic deformation of the contact space (Ruge 1993 ) (see Fig. 1 ). Figure 6 . Schematic diagram exhibiting the mechanism of the oxidation process and the oxide film construction on zircaloy. Figure 5 .
In PWRs the closure of the gap between the pellet and the clad takes about one full power yr whereas the hole is maintained for an extended period in BWRs. Due to the collapsible clad design of PHWRs, contact between the pellet and the clad is established right from the start of the lifetime of the fuel factor. Laser coating or laser cladding can be used to regionally functionalize metallic elements. In this course of, an edge layer of usually 0.1 to 2 mm is applied to the element. The coating materials employed is either powder or wire, or utilized in advance as a tape.
These approaches have encountered issues, together with porosity of the cladding, uneven cladding thickness, dilution of the cladding alloy because of the big heat enter required, and distortion of the workpiece by the excessive warmth enter. Laser cladding has decreased these problems and produced cladding layers with good uniformity, good dimensional management, and minimal dilution of the cladding alloy. provides a survey of a cladding tools. If the incoming strips must be heated so as to lower the energy of materials, this must be accomplished as close as attainable to the rolling hole and in a protecting environment so as to avoid oxidation of the cleaned and roughened surfaces. We provide excessive-quality decorative products that improve any house and interior.
The first identified use of cladding was in 1936
Increased put on and oxidation resistance of titanium aluminide alloys by laser cladding Euro Superalloys. Increased wear and oxidation resistance of titanium aluminide alloys by laser cladding. A structured separating layer, consisting of a 3-layer vapour-permeable roof underlay membrane with self-adhesive butyl strips, bonded to monofilaments organized in a random community, to be used as a spacer layer between the roof construction and the metal cladding. Those areas subjected to excessive heat - from the exhaust manifold or catalytic converter for example - would be insulated by a refractory material and metal cladding. Wire-primarily based laser deposition welding is a fabric-environment friendly 3D printing process for the manufacturing of metallic elements.
With it, we course of individual elements in addition to series components, inside in addition to outer contours, new and used elements. Cladding in building is material utilized over one other to supply a skin or layer and used to supply a degree of thermal insulation and weather resistance, and to enhance the looks of buildings. Between the cladding and the wall there is a cavity where rain can run down. Laser cladding with the aid of energy-based mostly or wire-formed filler supplies can be utilized for repair work, the application of damage and corrosion safety and the manufacturing of 3D parts (additive manufacturing).
is produced and the risk of a massive secondary hydriding failure is increased. In response to this unexpected consequence, several fixes were introduced.
The constants a and b are primary properties of the material and could be determined from standard laboratory experiments on recent gas. In explosive welding, a compression force created by detonation of explosives is used to affix overlapping steel sheets. The becoming a member of elements are organized in direction of one another at an angle of 1–15°, depending on the material and methodology, and are ready with a layer of explosive on the top. After ignition the becoming a member of areas are moved against one another at excessive velocity.
As the oxide layer grows, the compressive stress at the outer layer of oxide is not sustained and consequently the tetragonal phase turns into unstable and transforms into the monoclinic section. Such a metamorphosis causes the formation of a nice interconnected porosity within the oxide movie which permits the oxidizing water to return involved with the steel floor. With the event of an equilibrium pore and crack structure within the oxide layer, the oxidation rate effectively becomes linear, a attribute feature of the post-transition oxidation habits.
The low burnup habits is managed by elements corresponding to pellet densification and fuel-clad gap closure, but at larger burnups conductivity degradation becomes increasingly important, driving the temperatures up to and beyond the level the place gaseous and volatile fission merchandise start to be launched from the fuel. The penalties of this are thought-about further in later sections. because of their corrosion resistance to acids and bases and their low neutron-absorption charges. Zircaloys have anisotropic physical, mechanical, and chemical properties. Within the oxide layer, the alloying components influence the atomic transport such that the alloying focus determines the corrosive habits, with high alloying concentrations (above ∼0.6%) providing safety against oxide growth.
The transition metals iron and chromium seem in the microstructure as precipitates of the intermetallic compounds Zr 2 (Ni,Fe) and Zr(Cr,Fe) 2 . These minor alloying components improve corrosion resistance to an extent depending on the dimensions of the precipitates. Laser cladding has been applied to hardening of steam generator turbine blades and reached pilot production status [four ]. The blades had a machined pocket, into which powdered cobalt-primarily based metallic (Stellite 6) was fed forward of the laser beam.
Dissolved oxygen in PHWR coolant is controlled between 10–50 ppb and it has been observed that corrosion in each zircaloy-2 and Zr-2.5 Nb pressure tubes rises to an exceptionally excessive value at high oxygen concentrations. The BWR coolant usually contains a better stage of oxygen, usually 200–400 ppb.
In one, a second inner-floor liner of ordinary Zry is extruded on the sponge zirconium liner so as to restore corrosion resistance. In different modifications, the sponge zirconium is alloyed with iron or tin to improve oxidation resistance without affecting the softness that gives immunity from PCI. Standard Zry is sufficiently onerous to be susceptible to emphasize-corrosion cracking (SCC) when the pellet–cladding hole closes and the swelling gas generates substantial tensile hoop stresses within the cladding. In the presence of an aggressive fission product (iodine is most often cited), a brittle crack may be initiated and penetrate the cladding wall.

sheet steel Imitation Wood Cladding cladding n —
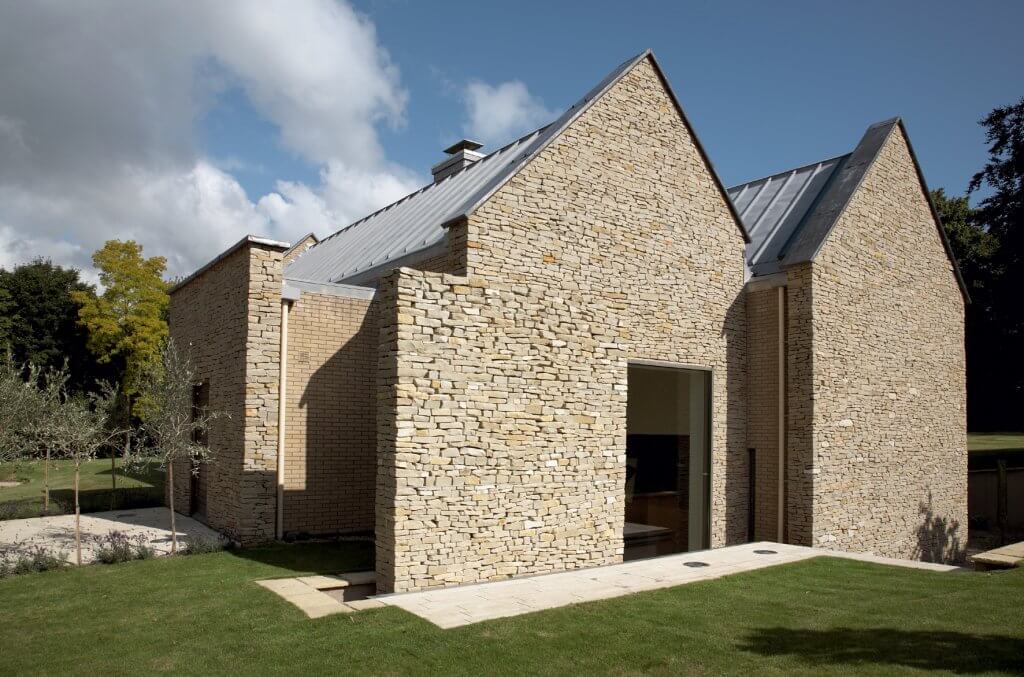
Long-time period, in-reactor, oxidation, and hydrogen decide up habits of zircaloy-2 and Zr-2.5Â Nb strain tubes, exhibiting parabolic after which accelerated linear oxidation and hydrogen pickup kinetics in zircaloy-2. A low and uniform price of corrosion and hydrogen choose up is seen in the in Zr-2.5Â Nb alloy. Differential swelling between cladding, wrapper tube, and spacing system (spacer wire or grids) can induce extra stresses and deformations on these parts and/or generate coolant move perturbations in the bundle. These phenomena have been studied and have particularly shown that wires or grid materials should be chosen and specified in order to reduce differential swelling.
Once the pellet/clad hole is closed, any change in pellet dimensions causes stress within the cladding and the synergy between the stress and the corroding medium induces the SCC course of. In order to stop or decrease pellet/clad interactions, each mechanical and chemical, a coating of graphite powder is utilized on the inside floor of cladding tubes.
The helium filling gas is also a fairly good conductor, but solely as long as it stays uncontaminated by fission merchandise. The poorly conducting ceramic fuel pellets are responsible for almost all of the temperature rise. The evolution of the conductivities of the pellet and filling fuel decide how the thermal efficiency develops with burnup.
Moreover, embrittlement owing to irradiation or temperature has to be mastered in order to avoid rupture within the reactor or during the back-finish of the cycle (handling, washing, etc.). Cold-labored austenitic steels (with composition closed to that of the cladding) had been used first but are now frequently changed by more swelling-resistant ferritic–martensitic steels (9Cr sort), in as far as the height wrapper temperature, decrease than that of cladding, permits avoidance of thermal creep problems.
The compromise between these competing demands has produced wall thicknesses of ∼0.9mm in BWRs and ∼0.7mm in PWRs. Laser cladding often includes covering a comparatively cheap substrate materials with a dearer alloy that may improve the resistance of the part to put on or corrosion.
With it, we process individual elements in addition to series components, internal in addition to outer contours, new and used parts. Cladding in development is material utilized over another to provide a pores and skin or layer and used to offer a level of thermal insulation and climate resistance, and to enhance the appearance of buildings. Between the cladding and the wall there is a cavity where rain can run down. Laser cladding with the aid of power-based mostly or wire-shaped filler supplies can be utilized for restore work, the applying of wear and tear and corrosion safety and the production of 3D parts (additive manufacturing).
Alloying elements, notably tin, niobium, and iron, current within the α-strong answer strongly affect each the kinetics and the mechanism of oxide development in zirconium alloys. ions from the environment to the reaction front on the steel/oxide boundary.
The thickness of the cladding may differ between zero.1 and 30 mm and the detonation velocity is between 1200 and 7000 ms −1 . The prime plate hits the underside plate with a pace of 100–1000 ms −1 , and pressures are within the range of 10 to one hundred kbar. Under sure circumstances a superheated layer of fabric forms in the contact space. The joint is then attributable to a deformation-induced melting bathtub.
In PWRs the closure of the gap between the pellet and the clad takes about one full power 12 months while the hole is maintained for a longer period in BWRs. Due to the collapsible clad design of PHWRs, contact between the pellet and the clad is established proper from the beginning of the lifetime of the gas factor. Laser coating or laser cladding can be used to regionally functionalize metallic parts. In this process, an edge layer of typically zero.1 to 2 mm is applied to the element. The coating materials employed is both powder or wire, or applied upfront as a tape.